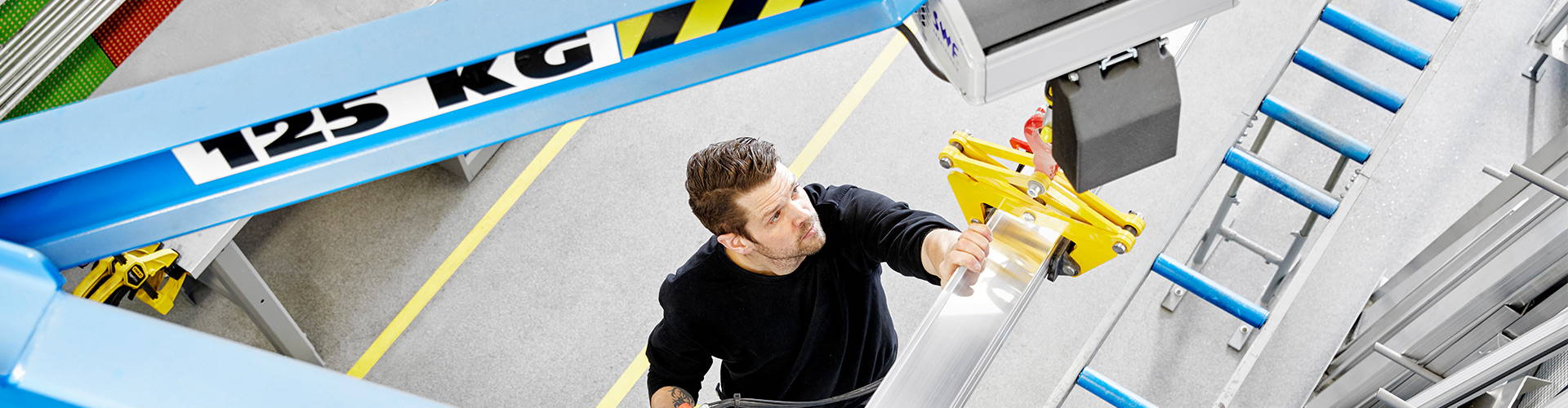
Risk assessment with lifting devices - important for safety
A common denominator for many lifting-related accidents is a lack of risk assessment. Continuously working with risk assessments and having a high level of safety awareness is therefore of great importance when working with any type of lifting equipment. We have gathered some tips on what is good to consider in connection with risk assessments.
Fixed/mobile lifting device
Using a fixed lifting device usually involves one type of lifting and in the same type of environment. In this case, a thorough risk assessment needs to be carried out before the equipment is used and then checked regularly. If the same equipment is to be used for a different type of lifting, a new risk assessment should ideally be carried out.
However, if you use a mobile device, you will need to carry out a new risk assessment each time, as the lifts can be very different.
When, how and who
To ensure that risk assessments do not fall through the cracks, it is important to establish procedures for how often they should be carried out, how they are done and who is responsible for ensuring that they are done. In addition, the person responsible for the risk assessment needs to have the right documentation, such as summaries of checks and inspections, as well as information on how long the equipment has been in use, in order to be able to include wear in the assessment, and perhaps above all invisible wear - wear that is not always visible but which can, for example, lead to material failure even though the equipment is used properly.
Establish clear procedures and work continuously to ensure that they are followed. Many accidents are caused by a lack of safety procedures and awareness. Therefore, to succeed all the way, you need to make sure that all staff involved have the right knowledge and that safety procedures are applied. In short, it's about creating a safety-conscious culture in your company.
What you need to look at in your assessment
In AFS 2006:6, the Swedish Work Environment Authority has collected rules on how risk assessment should be carried out. These include the requirement that lifting equipment and lifting gear may only be used by persons with documented theoretical and practical knowledge in the field. They have also summarized some points that should be given special attention, such as the stability of the lifting device in different ground and weather conditions, access to risk areas and load coupling.
The assessment should also take into account the experience of those carrying out the work and how stressed or tired they are. Many accidents occur at the end of a shift, just before a break or at other times when the worker is compromising safety. There is also an increased risk if the work is to be carried out by newly trained and inexperienced staff or trainees.
Learn from the offers
When accidents occur, they are generally always investigated to some extent and measures are taken to prevent a similar accident from happening again. It is also important to remember to report incidents, i.e. undesirable events that could have led to an accident, in order to learn from them and include them in your risk assessment. If you fix what caused the incident, an accident risk is also removed.
Learn more about how to create a safety-conscious culture around lifting in your workplace - download our white paper.